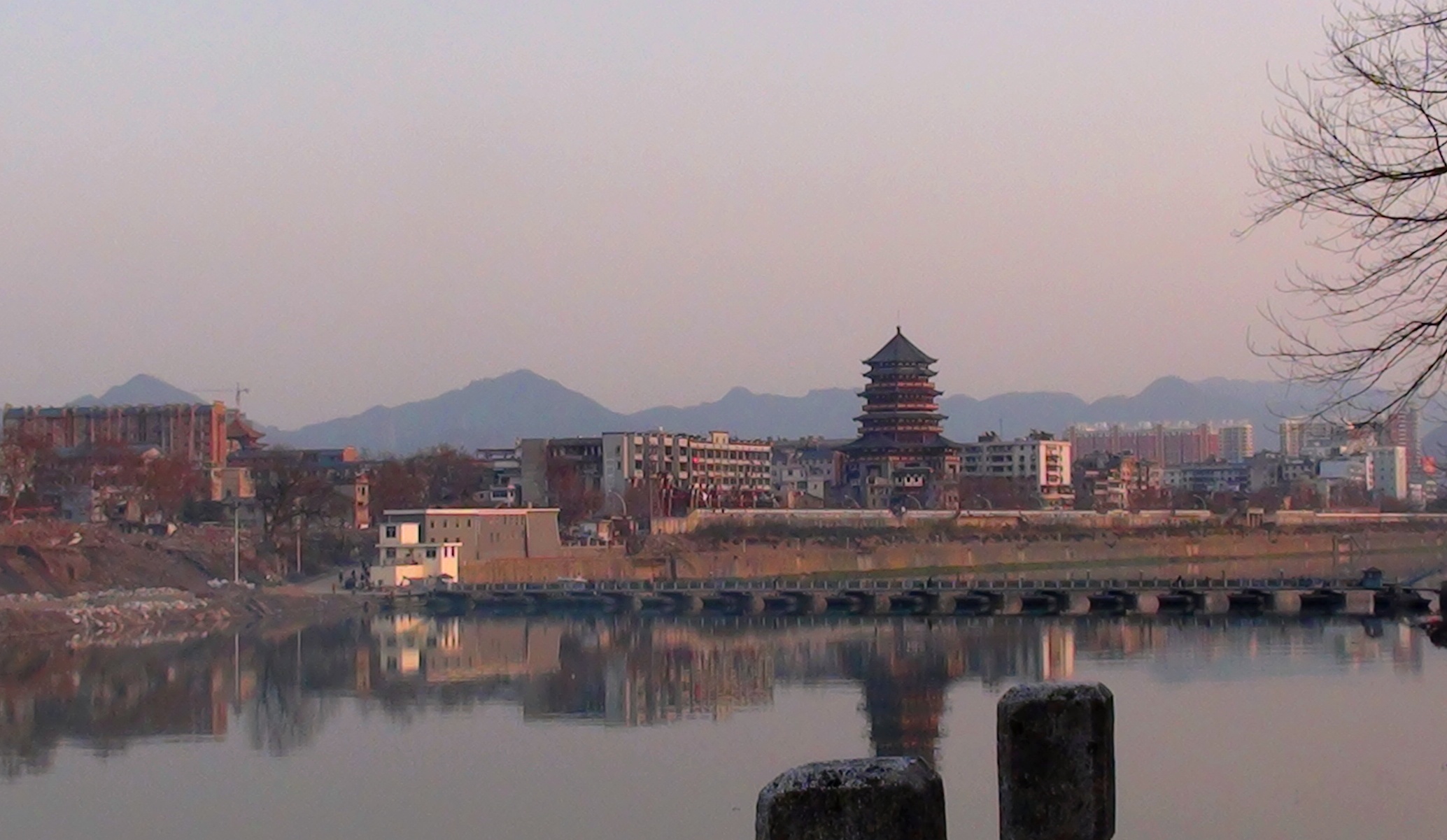
I had the extraordinary opportunity of having hands-on experience with Jingdezhen porcelain, taught by local craftsmen. In 2014, I was awarded the Windgate Fellowship Award. The $15,000 fellowships are annually given to 10 senior students, nationwide, working in the field of craft. The fellowship program is supported and administered by the Center for Creativity, Craft and Design, which is based in Asheville, N.C.
I used it to explore the origins of porcelain, evaluating the qualities of Asian wares and studying the commonly used materials, designs and production techniques of craftsmen in Japan and China. I also participated in a six-week residency at The Pottery Workshop in Jingdezhen, China’s porcelain capital. This was an invaluable experience that left a profound impact on my work.
The Pottery Workshop (PWS) was established in 1985 in Hong Kong and the Jingdezhen PWS has been operating in Jingdezhen since 2005. It is located in The Sculpture Factory, a place where sculptors and potters along with many other artisans congregate to create and fire everything made of fine Chinese porcelain. During my residency, I took the following classes:
- Qinghua Painting: History of blue & white porcelain, specialized tools for application, how to prepare qinghua for painting, and various painting techniques.
- Practice on greenware tiles and plates
- Over Glaze Painting Various materials (e.g. xincai, fencai) and techniques
- Carving Introduction to various carving techniques.
- Throwing & Trimming
- Mold-making: Plaster types, plaster mixing, single and multi-part molds.
- Slip Casting & Press Molding
The History of Jingdezhen Porcelain
Han Dynasty (206-220 BC)
Ceramics were produced in Jingdezhen as far back as the Han dynasty. At the time, the city was called Xinping. On the base of workmanship of Shang and Zhou dynasty, people in Jingdezhen made “blue pottery with glaze”. Pottery clay was in ample supply all around the town. The Gaoling mountain, 40 kilometers to the northeast, is one of the few areas in China which provided pure kaolin, one of the essential ingredients for porcelain. Other nearby areas such as Nankang, Sanbaopeng, Dongliu and Liujiawan provided the other ingredient; the so-called ‘China stone.’
Jin Dynasty (265-420)
During Jin dynasty, a craftsman named ZhaoKai made great contribution to the progress of porcelain quality, so he was called the “the master of porcelain making”. With the development of times, prosperity of the economy in east China, and the improvement of technique of making porcelain, Jingdezhen porcelain was sold to all of China.
North and South Dynasties (420-589)
In AD 583, the emperor of Nan dynasty, Chen Shubao (also known as Chen Hou Zhu) ordered to make a porcelain pillar for the villa in Jingdezhen.
Sui Dynasty (581-618)
Emperor Yang asked for lion and elephant ceramic sculptures for the palace.
Tang Dynasty (618-907)
The city was renamed Changnanzhen (Changnan Town), since it sits at the South bank of Chang river. And “china” is translated from “Changnan” (also known as Changnan).
After the foundation of Tang Dynasty in the reign of Li Yuan, ceramic production developed further. Two famous men, Tao Yu and Huo Zhongchu, appeared. Tao kilns were already making high-fired pottery, then known to be translucent and often referred to as ‘artificial jade. Tao Yu took this ceramic to the ruler of kingdom and thus, Changnan ceramics were known all over the China. Guangzhou in southern China became home to a large Arab community with its own mosques and trading houses who appreciated this porcelain style.
The Five Dynasties (907-960)
During the Wudai period, besides celadon wares, Jingdezhen was the first place to produce white wares, and there were a large number of kilns. The quality exceeded that of the famous Yue kiln and Jingdezhen gained the most prominent position in ceramics at the time. During the 1950s the kiln sites of Wu Dai were found in Huangnitou, Baihuwan,Tengmeiting and Hutian, demonstrating that during that period of time, porcelain was mainly celadon ware and white ware.
North Song Dynasty (960–1127)
By the time of the Song Dynasty, there were 5 famous kilns: Ru, Guan, Jun, Ding and Ge. The blueish white ceramics of Jingdezhen were well known nationwide.
In 1004, during the reign of Zhengzong, in the Jing De era, the emperor Zhao Huan ordered the city of Changnan to produce porcelain for the imperial family, with the character “made in Jing De period” on the bottom. Therefore the city changed its name to Jingdezhen, and its porcelain became famous throughout the country.
This did not mean that new kilns were built, but merely appointed established private kilns to add imperial wares to their production. The kilns were thus producing high quality wares for the imperial court at the same time as producing common dinner sets for the domestic markets.
During the end of the 11th century and the beginning of 12th century, because of the frequent wars, the famous kilns in the North declined.
South Song Dynasty (1127-1279)
After the Song dynasty moved their capital to the South, the political and economic centers were also moved to the South. A lot of craftsmen from the North came to Jingdezhen, which made breakthrough in the workmanship and scale. Jingdezhen entered a fast development stage, and became the “the town of porcelain”.
Jingdezhen porcelain became particularly important from the Song period with the production of Qingbai (青白, “Blueish-white”) ware. The Jingdezhen Qingbai was a transparent and jade-like type of porcelain, with a blueish-white glaze. Decoration was made by delicate carving or incising. The earliest piece of Chinese porcelain documented to have reached Europe, was a Qingbai porcelain bottle from Jingdezhen, which arrived in Europe in the middle of the 14th century: the Fonthill vase.
After receiving production requirements from the court, Jingdezhen would summon all the best ceramists together to design, choose and fire the best ware possible. This communal corroboration between the different potteries and kilns possibly lasted until at least the 15th century and beyond, when private kilns are known to have assisted official kilns with imperial orders.
According to the book Tao Ji written by Jiang Qi, at that time, Jingdezhen porcelain came from 300 distinct kilns.
Yuan Dynasty (1271-1368)
Besides continuing to produce the blueish white porcelain on large scale, the greatest invention during the Yuan rule was the blue and white porcelain. Before then, the ceramic decoration was dull. Cizhou potters from Hebei province migrated to the South and assisted in the technical and decorative achievements of porcelain making in Jingdezhen. The technique of painting with iron black oxides before glazing, so long practiced elsewhere in China, may have given birth to the first cobalt decorated wares of Jingdezhen, although underglaze cobalt decorated wares from the Gongxian kiln in Henan are known from Tang times. Blue and white started a new era and as soon as it appeared, it developed extremely fast.
In the history of porcelain making in Jingdezhen, a major issue that can not be neglected was that the establishment of Imperial Porcelain Factory (IPF). In order to meet the demands of emperor and the palace, a special agency serving the imperial family, the Fuliang Porcelain Office, was set up in Jingdezhen on 1278.
As for the process of the porcelain making, the important improvement was the addition of kaolin clay to the original pottery stones, which then increased the rate of aluminum. In this way, it raised the firing temperature, reducing the deformation rate and creating good conditions for making large-scale pieces.
When the blue and white was in its day, the porcelain workers of Jingdezhen also invented the underglaze red porcelain. People drew the copper red glaze on the porcelain body, and then put on the transparent glaze, fired in reducing atmosphere at high temperature. At last, the decoration showed the red color. In addition, Jingdezhen also produced red, green, yellow, three color glaze (sancai), eggshell, copper–red glaze, blue glaze and others.
Although large quantities of Jingdezhen porcelain were exported to Southeast Asia, India and the Middle East from the 9th century, it was the Yuan dynasty (1280-1368) under the rule of Kublai Khan that significantly expanded maritime trade. Marco Polo (1275-1292) wrote that Quanzhou harbor was the greatest port in the world.
Jingdezhen porcelain craftsmen introduced new forms and painted the earliest known untraditional Chinese motifs on high quality porcelain for foreign dignitaries. Porcelain that was customized to suit the needs of the Middle East included large plates with Islamic motifs.
Later, Jingdezhen produced Shufu ware, named after the two character inscription on some pieces. Shufu may mean the pieces were ordered for the Shumiyuan (Ministry of Defense). The Shufu pieces have a thick, somewhat opaque, glaze, almost white in color, with a faint blue-green tint.
From the mid-14th century, Jindezhen began to mass-produce blue underglaze porcelain.
Ming Dynasty (1368-1644)
During the Ming dynasty, Jingdezhen had become the center for porcelain making in China. Porcelain was produced in large quantities. Official kilns for Imperial productions were established in Jingdezhen. In the early Ming dynasty another 20 kilns in Jingdezhen were recognized for their quality wares and commissioned to produce ‘imperial porcelain’ exclusively for the court. These kilns were set up next to an ‘imperial depot’ in 1425 which was to assemble, store and arrange transport to Beijing and the imperial palace.
While production for overseas markets was reduced, private kilns in Jingdezhen made blue and white porcelain for the huge domestic market. Work for the official kilns was increased in 1433 when the Ming court ordered 443,500 pieces of porcelain for the imperial household. To fill this order, the number of official kilns was increased to 58.
Jingdezhen porcelain in the Ming dynasty reached its peak in all dimensions: quantity, quality, design and variety. Scientist Song Yingxing wrote in his famous book Tian Gong Kai Wu: “…several prefectures all together could not beat Jingdezhen in the aspect of porcelain production”. On the variety and color, its varieties were colorful and unprecedented.
The Porcelain Office in Jingdezhen produced wares for the palace, for diplomatic use and to be given as gifts. It relied on the authority of the emperor, gathering many craftsmen who were familiar with and good at porcelain making. The Porcelain Office invested large sums and used only the best materials in the porcelain production process, producing numerous excellent porcelain wares. Some of them were considered to be the national treasure. This Porcelain Office was set up in 14th century and lasted 500 years, 27 emperors from the Ming to Qing dynasty. It also made a great contribution to the development of Jingdezhen porcelain techniques.
At this time people in Jingdezhen invented thin-body porcelain, the porcelain writing board with different sizes, and imitation porcelain. Many famous porcelain artists come from this time. For example, Wu Hao was renowned for his thin-body porcelain wares. The “egg bowl” was considered to be one of the greatest products in the porcelain history. Zhou Danquan was famous for his imitation porcelain, which was like genuine and pursued by collectors heatedly at that time. Another one was Cui Guomao, whose works imitating the Xuan De and Cheng Hua kiln wares were called “Cui kiln Wares”.
As regards decorating, besides the blue and white, glazed color porcelain emerged and became a milestone in China’s ceramic history.
Qing Dynasty (1644-1911)
Because of the wars at the end of the Ming dynasty, Jingdezhen porcelain at the beginning of the Qing dynasty showed signs of
decline. But after 1680, porcelain production not only revived, but also started to make progress. Thanks to the hard work of the potters and craftsmen, porcelain wares made in Jingdezhen reached its peak during the period of Kangxi, Yongzheng, and Qianlong of Qing dynasty. A French Jesuit monk reported that there were over 3000 kilns in Jingdezhen at the time.
Jingdezhen porcelain in Qing dynasty had inherited the craftsmanship and variety of Ming Dynasty, but there were many inventions. For example, the blue and white at Kangxi period utilized gem blue, much purer and brighter than that of the Ming dynasty. These were the finest porcelains ever made. And what is more, many new glazes were invented at the time. In addition,
during the reign of Kangxi emperor, Jingdezhen resumed the production of copper red glaze, which had almost been lost since the
Ming dynasty.
With the Qing period, designs became more varied, combined folk and Imperial styles, and Jingdezhen ware became famous around the world.
Tang Ying, the ceramic superintendent, made significant contributions to development of Jingdezhen porcelain. He supervised porcelain production in Jingdezhen for 15 years, which made him the longest and most accomplished porcelain official. During his 15 year stay in Jingdezhen, Tang Ying did not place himself above the workers. instead, he modestly learned from them. When he first got to Jingdezhen, he knew nothing about porcelain making. After 3 years working and studying with craftsmen, Mr. Tang became an expert at porcelain making. Meanwhile, Tang Ying summarized the porcelain making technique scientifically. He wrote some books about porcelain, for example, On Pottery Issue, Illustrated Pottery Making, How to Make Pottery, Submitted Papers on
Porcelain and others. In special, the Illustrated Pottery Making was an important work on ceramic craftsmanship and culture (see below). The porcelain under his superintendency were called “Tang kiln”, reaching an unprecedented level in manufacturing and quality. He was familiar with the clay, carefully selecting the material , so his works were the best among the best.
In addition, other superintendents made their contribution to porcelain development in Jingdezhen. Zang Yingxuan, the superintendent from the 19th to 27th year of Kang xi period, was another example. His porcelains were called “Zang ware”, which had a complete set of colors. Liang Tengquan, the governor of Jiangxi province was also responsible as superintendent Jingdezhen’s porcelain production. He was an enthusiastic researcher. Nian Gengyao, of the Yongzhneng period, invented many new color glazes.
In later years, porcelain industry in Jingdezhen suffered setbacks. After Qianlong of Qing dynasty, porcelain making in Jingdezhen began to decline for various reasons. Porcelain production suffered damages due to the wars. Owing to instability in the political environment, and the flood of foreign products, the Porcelain Office that had lasted 500 years was closed.
Major Types of Jingdezhen Porcelain
Yaobian Porcelain
Yaobian vases feature a simple, natural shape combined with sophisticated colors. Their dominant purple glaze flows into cyan and moon white in a pattern that takes on a life of its own and enhances the beauty of the vase. Glazing the fired body of the vase multiple times, then baking at a low temperature creates such patterns. The copper, cobalt, titanium, manganese, and iron coloring elements combine to produce a variety of shades, mingling with the red glaze on the porcelain to create striking hues.
Celadon / Yingqing Porcelain
The production of monochromatic ceramics matured over several centuries in Northern China, achieving particular success with green-glazed or “celadon” pieces. These were developed as Ru, Guan, Ge, and Jingdezhen ware to a high level. The delicately lobed and rounded bodies of these porcelains reflect the mastery of the artisans from this period.
Blue & White Underglaze Porcelain
Drawing the design with cobalt pigment onto the stoneware body, and painting over it with a transparent glaze creates the blue-white style, also known as “underglaze blue”. The piece is then fired at a high temperature. Blue-white porcelain was introduced during the Yuan Dynasty and has been continuously in production ever since, thanks to is bright colors, simple yet elegant patterns, and smooth glaze that never fades.
Wucai Porcelain (also known as Gucai)
Wucai is a type of overglaze decoration. After firing the piece at a low temperature; red, green, yellow, blue and purple enamels are applied to the white ware. Wucai has been popular since the early Qing Dynasty. The technique has been famous for hundreds of years and is listed as a national intangible cultural heritage. The subject for Gucai painting is very limited, mainly including peach, leechee and pomegranate which are symbols of good luck. The colorful paintings on white porcelains will look bright after burned in furnace.
Doucai Porcelain
Docai Porcelains feature an unusual combination of exquisite patterns, color coordination, and well executed color filling. It reached its height in the Yonzhen and Kangxi reigns during the Qing Dynasty. The blue-white color is first applied under the glaze. Then red, green, and yellow are filled over the glaze and the piece is fired at low temperatures.
Famille Rose (Fencai, Yangcai)
Famille Rose was developed during the Kangxi reign of the Qing Dynasty, and is based on the Wucai and Docai styles. Famille rose porcelains feature complex, ornate patterns with a balanced tone, detailed drawing, and steady color.
Early Jingdezhen Porcelain Exports
There was a international market in Changan, the capital during Tang dynasty.Jingdezhen ceramics were first sold to Asian countries. Meanwhile, Jingdezhen porcelain also reached Europe.
During the expansion of Jingdezhen porcelain industry during the Yuan and Ming dynasties, exporting grew exponentially. During the early years of Ming dynasty, San Bao Eunuch, ZhengHe, reached over 30 western countries, leading the largest ocean fleet at that time, such as the NanYang archipelago, Persia and Arabia. In addition, people in America, Africa and Austrialia developed interest in Jingdezhen porcelain. It is recorded that during the Longqing period of Ming dynasty, between one and two million silver dollars flowed from Banco de Mexico to China every year, most of which were used to buy Jingdezhen porcelain.
Japanese Market
In the final decades of the Ming dynasty, the potters of Jingdezhen produced blue-and-white porcelain, kosometsuke, and an underglaze-blue and polychrome porcelain ware, ko’akae, for the Japanese market, particularly for use in the popular tea ceremony.
Portuguese Merchants
The Portuguese found Chinese porcelain first in India and then, after their settlement in Melaka was established in 1511, in China. The first pieces of Jingdezhen porcelain brought back to Portugal by ship were acquired in India and presented to King Manuel I by Vasco da Gama. Against imperial prohibitions, they managed to order porcelain from Fujian middlemen, and eventually they were forwarding drawings to Jingdezhen for specially designed pieces. with the emblem of King Manuel I (1495-1521), and various shapes decorated with other coats-of-arms. This shows how willing the Jingdezhen potters were to please new customers. The taste for Chinese porcelain in Portugal and elsewhere in Europe slowly gained popularity during the later part of the 16th century when the Portuguese royalty gifted other European nobilities with this exclusive commodity which they alone could acquire at source.
The Dutch Traders
Export production at Jingdezhen witnessed yet another boost when the Dutch arrived in China in the early 17th century. They had repeated disputes with the Portuguese and the Chinese administration. Misbehaving, as the Portuguese did before them, the Dutch were forced to trade along the Chinese coast and from various illegal settlements with primarily Fujian merchants. From their various illegal bases on China’s coast, on Taiwan, and at later establishment in Japan, the Dutch had to wait a full year for their deliveries. Yet, despite the distance and with unprecedented trust in the Chinese middlemen, the Dutch alone already in 1608 ordered more than 108,000 pieces of porcelain, a number that grew to 355,800 pieces in 1644, for the European market alone.
The Export Routes
All Jingdezhen porcelain began their long journeys on the Chang River loaded on small river boats. River transport was without doubt long and cumbersome. Crews rowed long distances against the current
and often used poles to push the heavily loaded boats though shallows and rocky streams. In addition to this
work and responsibility, whether they started upstream or downstream, they had to return to their original
place of loading before repeating the journey. From coastal ports in Zhejiang, Fujian and Guangdong, Ming and Qing dynasty porcelain reached Chinese
merchants and shippers who supplied the Spanish in the Philippines, the Portuguese in Guangzhou and
Macao, and the Dutch in Taiwan and later Japan.
Key Factors Contributing to Jingdezhen’s Porcelain Excellence
Raw Materials
Jingdezhen is located in the Northeast of Jiangxi Province, belonging to the subtropical monsoon climate area. The rainfall, the source of water, illumination and forest reserves are sufficient. The East River, South River, West River and little North River, flow through the urban area from North to South.
Kaolin produced nearby is the high quality raw material for porcelain production. Kaolin clay was already used in Yuan dynasty. Nowadays, the name of Kaolin village has become the universally accepted mineralogical name of porcelain clay.
Craftsmen
After the fall of the Northern Song dynasty, most outstanding porcelain craftsmen from the famous Ru, Ding and Jun kilns moved to the South, contributing to Jingdezhen porcelain technique with their knowledge. Jingdezhen porcelain makers were so good at learning from others that they could absorb advanced porcelain making techniques from other parts of the country and even from abroad that they could make their own innovations and advancements.
There was a very careful division of labor. The process from clay to a finished product involved the participation of 72 people.
Owing to the this, workers were able to become skillful through a long time of practice.
There was traditional respect for teachers and deep concern about artists’ morality. In Jingdezhen, “Master” is the most common
form of address. Those who want to formally become a pupil to a master, must obey strict guild regulations. Only the highly skilled could be rich in wealth and high in social status.
An environment of healthy competition between official kilns & folk kilns fostered continuing advances in technological level.
Funding
The emperors set up the Porcelain Office in Jingdezhen to produce items for palace use. The emperor invested heavily. What is more important, large quantities of porcelain wares were sold to foreign countries. As the funds continued to flow, Jingdezhen was capable of constantly producing and increasing its capacity .
Technological Achievements
A book written in Qing dynasty entitled Record of Jingdezhen’s Porcelain, truly described how the traditional techniques were developed.The following are the main achievements featuring Jingdezhen porcelain making.
With the increasing improvement of techniques of form making, press mould forming,trimming and glazing. In the Ming dynasty, a variety of porcelain products which varied in size from small egg-shell cups to one-meter big dragon jars could be made, and the techniques of sculptured porcelain products reached exceptional quality.
In the Tang dynasty, earliest forms of Blue-and-white porcelain could be found in the remains of some kilns, but firing better blue-and-white porcelains in Jingdezhen began in the Yuan Dynasty. Furthermore, Jingdezhen was also the original place where blue-and-white porcelain became one of the main streams of Chinese porcelain.
In the long history of porcelain-making, Jingdezhen’s porcelain firing kiln was a good combination of both Dragon shaped kilns popular in the south and U-shaped kilns popular in the north and was then developed into Jingdezhen Kiln which was later called the egg-shaped kiln. This marked the highest level of that time in the building of traditional kilns and firing techniques.
In the eighth year of Qianlong Emperor of Qing Dynasty (1743), Porcelain-Making Supervisor – Tang Ying was appointed by the Emperor to compile An Illustrated Book on Porcelain Making (20 chapters). In this book, the technological process of porcelain making was vividly explained and described. The book summarized technological achievements of Jingdezhen porcelain industry in full bloom as a sequel to Jiang Qi’s Record of Porcelain Making and Song Yingxing’s Tian Gong Kai Wu which had respectively recorded Jingdezhen porcelain making.
Jingdezhen Porcelain Educational and Research Institutes
In present day, Jingdezhen hosts numerous porcelain oriented educational institutions:
- Jingdezhen Ceramic Institute: the only ceramic higher education institution
- The Ancient Ceramic Research Institute
- The Ceramic Designing Institute of Jingdezhen, the only national professional porcelain design institute
- The Porcelain Hall
- The Ancient Porcelain Association
- The Ceramic Association
- The Kiln Association
- The Ceramic History Research Association
- The Ceramic Fine Arts School
- The Ceramic Technical School of Jingdezhen
- The Industrial Ceramic Department of Technical School of Jiangxi Province
- The Ceramic Artistic Research Institue Center of the Commission of Light Industry
- The Ceramic Research Institute of Jiangxi Province
- Jingdezhen Ceramic Research Institute
- Jingdezhen Pottery Archaeological Research Institute
- The Ceramic History Museum of Jingdezhen
- The Ceramic Museum of Jingdezhen
- Jingdezhen Folk Kiln Artistic Advanced Study and Training Institute
Because of the establishment of these institutes, schools, museums and associations, Jingdezhen formed a complete network of scientific research and ceramic education with its unique characteristics.
Jingdezhen Porcelain Composition
The two essential components in Jingdezhen porcelain are mixed in different proportions depending of the type of ware desired. The first of the ingredients is kaolin, a pure white clay formed by the decomposition of aluminum silicates. Kaolin remains white when fired, but its low plasticity makes it difficult to pot. It is washed in successive ponds until obtaining an impurity-free product and shaped in to bricks. The second ingredient is China stone (petuntse), a granitic grayish white stone, which is pulverized by water driven pestles, washed and dried into bricks.
The kaolin-petuntse mixture is white and plastic and when used with for blue and white wares, is fired at 1,250-1,330˚ Centigrade.
Both materials were quarried in mines outside Jingdezhen by specialized mills and transported by river boats to the potteries.
At Jingdezhen potteries the two different kinds of brick were mixed with water and homogeneized before storage in earthenware jars. The proportions of the two substances depended on the type of ware to be made. For finer wares, more kaolin was required; this allowed the shape to remain secure during firing. On the other hand, petuntse was required for translucency, so characteristic for porcelain.
Twenty Illustrations of the Manufacture of Porcelain, by Tang Ying 1745
What follows is the full text of the “Twenty Illustrations of the Manufacture of Porcelain” written by Tang Ying, the celebrated superintendent of the porcelain manufacture in the province of Jiangxi during 1736-1753. This text was written on Imperial command in 1743 and is widely reprinted. The most authentic version is to be found in the official annals of the province of Jianxi, Book XCIII, folio 19-23. This text is immediately based on the translation that was made by S.W. Bushell in 1899.
1. Mining the clay and Pulverizing to muddy consistency 采石制泥
“In the manufacture of porcelain the body is formed of molded earth. This earth is prepared from stone, which must be mined and purified for the purpose. The stone is found in the province of Kiangnan, within the prefecture Hui-chou Fu, at Ch’i-men-hsien, which is two hundred li distant from the porcelain manufactory.
The two mountains called P’ing-li and K’u-k’ou, in this district, both produce the white stone. It is obtained by mining, and when broken exhibits black veins branching like the deer’s-horn seaweed.
The natives take advantage of the mountain torrents to erect wheels provided with crushers. Having been finely pulverized, it is then purified by washing and levigation, and made up in the form of bricks, which are called pai-tun or “white bricks” (petuntse). When the color is uniform and the texture perfectly fine, it is used for the making of the round pieces and vases of eggshell and of pure white porcelain, and of similar objects decorated in blue.
Besides this there are several other kinds of earth called Kao-ling, Yu-hung, and Ch’ien-t’an, after their different places of production, which are all situated in the province of Kiangsi, within the bounds of the prefecture Jao-chou Fu. They are dug out and prepared in the same way as the petuntse, and can only be used for mixing with this last, or in the making of coarser and thicker ware.
2. Processing and purifying the muddy clay 淘炼泥土.
In porcelain-making the first requisite is that of washing and purifying the materials of the paste, so as to make it of fine homogeneous texture. The presence of “stars” or of fragments of stone would cause flaws in the porcelain. Foreign particles or loose paste would lead to cracks.
The method of purifying the paste is to mix the materials with water in large earthenware jars, and to stir the mixture with wooden prongs, so that it remains suspended in the water while the impurities sink to the bottom.
The paste is then passed through a fine horsehair sieve, and next strained through a bag made of a double layer of silk. It is then poured into a series of earthenware jars, from which the water is run off, and the paste is left to become solidified. A wooden box with no bottom having been placed upon a pile composed of several tiers of new bricks, a large cloth of fine cotton is spread inside, and the solidified paste is poured in, wrapped round with the cloth and pressed with more bricks, which absorb all the water.
The prepared paste, freed from the superfluous water, is then thrown on to large stone slabs and worked with iron spades until it has become perfectly compact and ductile, and fit for the manufacture of porcelain.
All the different kinds of paste are prepared in the same way, the various materials having been mixed in definite proportions according to their different properties.
3. Processing of ashes to formulate glazes 炼灰配釉
“All kinds of porcelain require glaze, and the composition used for glazing can not be prepared without ashes. The ashes for the glaze come from Lo-p’ing-hsien, which is one hundred and forty li to the south of Jingdezhen.
They are made by burning a gray-colored limestone with ferns piled in alternate layers. The residue – after it has been washed thoroughly with water – forms the ashes for the glaze.
The finest kind of petuntse made into a paste with water is added to the liquid glaze ashes, and mixed to form a kind of purée, the proportions being varied according to the class of porcelain.
Within the large jar, in which the mixture is made is placed a little iron pot, through the two handles of which a curved stick is passed, to make a ladle for measuring the ingredients. This is called a p’en. For example, ten measures of petuntse paste and one measure of ashes form the glaze for the highest class of porcelain. Seven or eight ladles of paste and two or three ladies of ashes form the glaze for the middle class. If the paste and ashes are mixed in equal proportions, or if the ashes are more than the paste, the glaze is only fit for coarse ware.
In the picture the little iron pot which is seen floating inside the large jar is the p’en or, measure.”
4. Making of fire-resistant clay boxes 制造匣钵
“The porcelain while being fired in the furnace must be kept perfectly clean: a single spot of dirt makes a colored stain. Moreover, the blast of air and fierce flames of the furnace would injure the delicate paste.
For these reasons it is necessary to place the porcelain inside saggars. The clay used in making these cases comes from the village of Li-ch’un, which is on the northeast of Jingdezhen. It is of three different colors – black, red and white.
A kind of blackish yellow sand, which is found at Pao-shih-san, is mixed with the clay to form a paste, so that it may be more readily fired.
The cases are fashioned on a wheel, which is similar to the wheel used for porcelain.
The paste need not be finely levigated. After the cases have been partially dried they are roughly finished off with a knife, put into the furnace, and fired for the first time empty. When baked and ready for use, they are called by the name of tu-hsia, or ‘finished cases’.
The workmen who manufacture the saggars are used to – with the same coarse paste – to make, on the same wheel, a supply of earthenware bowls for the daily use of the potters in their native hamlets.”
5. Molding 圆器修模
“In the manufacture of the round ware each several piece has to be repeated hundreds or thousands of times. Without molds it would be most difficult to make the pieces all exactly alike.
The molds must be made in accordance with the original design, but the size can not be so precisely measured; they must be larger than the model, otherwise the piece will come out smaller than the pattern.
The raw paste, which is expanded and loose in texture, becomes during the process of firing contracted and solidified to about seven or eight tenths of its original size, a result following from the natural laws of physics.
The proper proportionate size of the unbaked piece is fixed by the mold, and therefore the molders use the term ‘prepare’ instead of ‘make’. Each piece must have several molds prepared, and the size and pattern of the contents when taken out of the kiln must be exactly alike.
A good practical knowledge of the length of firing required and of the natural properties of the paste is necessary before it is possible to estimate the exact amount of shrinkage, so as to fashion the molds of the proper form. In the whole district of Jingdezhen there are only three or four workmen reputed clever at this special handiwork.”
6. Throwing 圆器拉坯
“There are several different processes of work in the manufacture of this round ware. The square, polygonal, and ribbed pieces, and those with projecting corners, have to be carved, engraved, molded, and finished with the polishing knife, all of which are different branches of work.
The plain round pieces are turned on the wheel, being distributed according to their size between two classes of workmen. The first take the large pieces and fashion the round dishes (p’an), the bowls (wan), the cups (chung), and the saucer-plates (tieh), from one up to two or three feet in diameter; the second make on the wheel the same kind of pieces which measure less than a foot across.
The wheel consists of a disk of wood mounted below upon a perpendicular axle, so as to revolve continuously for a long time, during which the piece must be properly turned, without becoming too thick, too thin, flattened, or otherwise misshapen. There is a carpenter at hand to repair it when necessary.
Beside the wheel is an attendant workman, who kneads the paste to a proper consistency and puts it on the table. The potter sits upon the border of the framework and turns the wheel with a bamboo staff.
While the wheel is spinning round he works the paste with both hands; it follows the hands, lengthening or shortening, contracting or widening, in a succession of shapes.
It is in this way that the round ware is fashioned so that it varies not a hair’s breadth in size.”
7. Carving into Forms and Body works 琢器做坯
“The vases and sacrificial vessels, called p’ing, lei, tsun, and yi, are comprised in this general name of cho ch’i. The plain round vases are fashioned upon the potter’s wheel, in the same manner as the ordinary round ware; they are then dried in the open air and turned on the polishing wheel to be finished with the knife.
After the vase has been thus shaped it is washed with a large goat’s-hair brush dipped in water, till the surface is perfectly bright and spotlessly clean. After this the glaze is blown on, it is fired in the kiln, and comes out a piece of white porcelain. If painted in cobalt on the paste and then covered with glaze, it is apiece decorated in blue.
In making the carved polygonal, ribbed, and fluted vases, the paste, wrapped in cotton cloth, is pressed with flat boards into thin slabs, which are cut with a knife into sections. The pieces are joined together by some of the original paste diluted with water.
There is another kind of vase which is made by the process of molding, and which is finished after it is taken from the mold in the same way.
The carved polygonal vases and the carved molded vases have to be filled in and washed clean with the brush in the same way as the round vases turned upon the wheel.
All the varied forms of vases may be engraved with the style, or embossed in relief, or carved in openwork designs, for which purposes, when sufficiently dried, they are given to artificers specially devoted to these several branches of work.”
8. Extracting Blue hue 采取青料
“All kinds of porcelain, whether round ware or vases, that have to be decorated in blue, whether modeled after that of the reigns of Xuande, Chenghua, Jiajing, or Wanli, require this blue color for the painting of their decoration.
The deep blue monochrome glaze also requires this blue for its preparation.
The material comes from the province of Chekiang, where it is found in several mountains within the prefecture’s Shao-hsing Fu and Chin-hua Fu.
The collectors who go into the hills to dig for it wash away the earth that adheres to it in the water of the mountain streams. The mineral is dark brown in color. The large round pieces furnish the best blue and a called ‘best rounds,’ distinguished in addition by the name of the place of production.
It is brought by merchants to the porcelain manufactory, and is buried by them under the floor of the furnace roasted for three days, and washed after it is taken out, before it is finally offered for sale, ready for use.
The material is also found in different mountains in the provinces of Kiangsi [Jiangxi] and Kuangtun [Guangzhou] but the color produced by these kinds is comparatively pale and thin, and it is unable to supply the fire, so that they can be used only in painting coarse ware for sale in the market.
The picture exhibits only the collection of the material: the processes of preparation and roasting are not shown.”
9. Processing and purifying the formulated blue hue 炼选青料
“The blue material, after it has been roasted, must be specially selected, and there is a particular class of workmen whose duty it is to attend to this. The superior kind selected is that which is dark green in color, of rich translucent tint and brilliant aspect. This is used in the imitation of antiques, for the monochrome blue glaze, and for fine porcelain painted in blue.
When of the same dark-green color, but wanting somewhat in richness and luster, it is used for the decoration of the coarser porcelain made for sale. The remainder, that has neither luster nor color, is picked out and thrown away.
When the material has been selected it is ready for use. The method employed is to paint with it upon the piece that has not been fired, to invest the piece afterward with glaze, and then to fire it in the furnace, from which it comes out with the color uniformity transformed into a brilliant blue. If it has not been invested with glaze the color will be black. Should the piece be overfired, the blue of the painted decoration will ‘run’ into the white ground of the piece.
There is one kind of blue, commonly called onion sprouts, which makes very clearly defined strokes that do not change in the furnace and this must be selected for fine painting.
The picture shows baskets filled with boxes of the color, with an ordinary background; there is no actual reference in it to the selection of the color.”
10. Embossing materials on body work 印坯乳料
“After the large and small round pieces have been shaped on the wheel and have been sufficiently dried in the air they are put into the molds which have been previously prepared and are pressed gently with the hands until the paste becomes of regular form and uniform thickness.
The piece is then taken out and dried in a shady place till it is ready to be shaped with the polishing knives. The damp paste must not be exposed to the sun, as the heat would crack it.
With regard to the preparation of the color for the artists, it must be ground perfectly fine in a mortar; if coarse, spots of bad color will appear. Ten ounces of the material are put into each mortar, and a special class of workmen grinds it for a whole month before it is fit to be used.
The mortars used for grinding it are placed upon low benches, and at the sides of the benches are two upright wooden poles supporting cross-pieces of wood, which are pierced to hold the handles of the pestles.
The men, seated upon the benches, take hold of the pestles and keep them revolving. Their monthly wage is only three-tenths of an ounce of silver. Some of them grind two mortars, working with both hands. Those who work till midnight are paid double wages. Aged men and young children, as well as the lame and sick, get a living by this work.”
11. Blue and white paint work 圆器青花
“The different kinds of round ware painted in blue are each numbered by the hundred and thousand. If the painted decoration upon every piece is not exactly alike, the set will be irregular and spotted.
For this reason the men who sketch the outlines learn sketching, but not painting; those who paint study only painting, not sketching; by this means their hands acquire skill in their own particular branch of work, and their minds are not distracted. In order to secure certain uniformity in their work, the sketchers and painters, although kept distinct, occupy the same house.
As to the other branches of work – embossing, engraving, and carving in openwork – they are treated in the same way, and each is entrusted to its own special workmen. The branch of decorating in underglaze red, although really distinct, is allied to that of painting.
With regard to the rings round the borders of the pieces and the encircling blue bands, these are executed by the workmen who finish the pieces on the polishing wheel while the marks on the foot underneath and the written inscriptions, are the work of the writers who attach the seals.
For painting flowers and birds, fishes and water-plants, and living objects generally, the study of Nature is the first requisite; in the imitation of Ming dynasty porcelain and of ancient pieces, the sight of many specimens brings skill. The art of painting in blue differs widely from that of decoration in enamel colors.”
12. Painting on the body 制画琢器
“The different forms of vases and sacrificial vessels comprised in the general term of cho ch’i include the square, the round, the ribbed, and those with prominent angles. There are various styles of decoration executed by painting in colors and carving in openwork.
In copies from antiquity artistic models must be followed; in novelty of invention there is a deep spring to draw from.
In the decoration of porcelain correct canons of art should be followed; the design should be taken from the patterns of old brocades and embroidery, the colors from a garden as seen in springtime from a pavilion.
There is an abundance of specimens of the Kuan, Ko, Ju, Ting and Chun at hand to be copied; and water, fire, wood, metal, and earth (the five elements of physics) supply an inexhaustible fund of materials for new combinations of supernatural beauty.
Natural objects are modeled, to be fashioned in molds, and painted in appropriate colors; the materials of the potter’s art are derived from forests and streams and ornamental themes are supplied by the same natural sources.
The sacrificial wine-vessels, tsun and lei, are of equal importance; the censers, shaped like the ancient bronzes, yi and ting, emit flames of brilliant color.
In addition to the ancient earthenware drums (wa fou), many kinds of musical pipes are now made, and the artistic skill of the color-brush perpetuates on porcelain clever works of genius.”
13. Glazing by blowing or touching 蘸釉吹釉
“All the different kinds of round ware and vases, including the pieces decorated in blue, as well as the copies of Kuan, Ko, and Ju porcelain, must have the glaze applied before they are fired.
The ancient method of putting on the glaze was to apply it to the surface of the vase, whether square, tall, fluted, or ribbed, with a goat’s-hair brush filled with the liquid glaze, but it was difficult to distribute it evenly in this way.
The round ware, both large and small, and the plain round vases and sacrificial vessels used all to be dipped into the large jar which held the glaze, but they failed by being either too thickly or too thinly covered, and, besides, so many were broken that it was difficult to produce perfect specimens.
In the present day the small round pieces are still dipped into the large jar of glaze liquid, but the vases and sacrificial vessels and the larger round pieces are glazed by the soufflé process. A bamboo tube one inch in diameter and some seven inches long has one of its ends bound round with a fine gauze, which is dipped repeatedly into the glaze and blown through from the other end. The number of times that this process has to be repeated depends partly on the size of the piece, partly on the nature of the glaze, varying from three or four times up to seventeen or eighteen.
These are the two distinct methods of glazing: by immersion and insufflation.”
14. Using knife to retouch the body & foot base 镟坯挖足
“The size of the round piece has been fixed in the mold, but the smooth polish of the surface depends on the polisher, whose province is another branch of work, that of ‘turning.’
He uses in his work the polishing wheel, which in form is like the ordinary potter’s wheel, only it has projecting upward in the middle a wooden mandrel, the size of which varies, being proportioned to that of the porcelain which is about to be turned. The top of this mandrel, which is rounded, is wrapped in raw silk to protect the interior of the piece from injury. The piece about to be turned is put upon the mandrel, the wheel is spun round, and it is pared with the knife till both the inside and outside is given the same perfectly smooth polish. The coarser or finer finish of the form depends upon the inferior or superior handiwork of the polisher, whose work is consequently of great importance.
With regard to the next process, that of scooping out the foot, it is necessary, because each piece, when first fashioned upon the potter’s wheel, has a paste handle left under the foot two or three inches long, by which it is held while it is being painted and glazed.
It is only after the glazing and the painting of the decoration are finished that this handle is removed by the polisher, who at the same time scoops out the foot, after which the mark is written underneath.
In the picture the workmen are seen occupied in the two processes of polishing the surface and scooping out the foot.”
15. Preparation for firing 成坯入窑
“The kiln is long and round, and resembles in shape a tall water-jar (weng) turned over on its side. It measures a little over ten feet in height and breadth, about twice as much in depth. It is covered with a large, tiled building which is called the ‘kiln-shed.’ The chimney, which is tubular, rises to a height of over twenty feet behind, outside the kiln-shed.
The porcelain, when finished, is packed in the saggars and sent out to the furnace men. When these men put it in the kiln they arrange the saggars in piles, one above the other, in separate rows, so as to leave a space between the rows for the free passage of the flames.
The fire is distinguished as front, middle, and back; the front of the fire is fierce, the middle moderate, the back feeble.
The different kinds of porcelain are placed in the furnace according to the hard or soft quality of the glaze with which they are coated. After the kiln has been fully charged the fire is lighted, and the entrance is then bricked up, leaving only a square hole, through which billets of pinewood are thrown in without intermission.
When the saggars inside the furnace have attained a silvery red color (white heat) the firing is stopped, and after the lapse of another twenty-four hours the kiln is opened.”
16. Firing processes 烧坯开窑
“The perfection of the porcelain depends upon the firing, which, reckoning from the time of putting in to that of taking out, usually occupies three days. On the fourth day, early in the morning, the furnace is opened, but the saggars inside, which contain the porcelain, are still of a dull-red color, and it is impossible to enter yet.
After a time the workmen who open the kiln, with their hands protected by gloves of ten or more folds of cotton soaked in cold water, and with damp cloths wrapped around their heads, shoulders, and backs, are able to go in to take out the porcelain.
After the porcelain has all been removed and while the furnace is still hot the new charge of ware is arranged in its place. In this way the new porcelain, which is still damp, is more gradually dried, and is rendered less liable to be broken into pieces or cracked by the fire.
The men in the picture who are leaning on the table wrapped in cloths are those that take the porcelain out of the kiln; the other men who are carrying loads of firewood are waiting to fire the next charge; the actual process of carrying out the contents of the furnace is not clearly indicated.”
17. Coloring paint work 圆琢洋采
“Both round ware and vases of white porcelain are painted in enamel colors in a style imitate from Western foreigners, which is consequently called Yang ts’ai, or ‘Foreign Coloring.’
Clever artists of proven skill are selected to paint the decoration. The different materials of the color having been previously finely ground and properly combined, the artist first paints with them upon a slab of white porcelain, which is fired to test the properties of the colors and the length of firing they require.
He is gradually promoted from coarse work to fine, and acquires skill by constant practice; a good eye, attentive mind, and exact hand being required to attain excellence.
The colors which are employed are the same as those used for cloisonné enameling upon copper (Fa-lang). They are mixed with three different kinds of medium, the first being turpentine the second liquid glue, the third pure water. Turpentine is best adapted for free coloring; glue is more suitable for thin washes, water for retouching the colors in relief.
While it is being painted the piece is either supported upon a table or held in the hand, or laid upon the ground, according to its size and it is laced in the position most convenient for the read use of the brush.”
18. Types of furnaces 明炉暗炉
“White paste porcelain that has been previously fired in the furnace is first decorated by the artist with painting in colors. When it has been painted in colors it must be again fired to fix the colors. For this purpose two kinds of muff le stoves are used, one kind being open, the other closed.
“The open stove is used for the smaller pieces. This stove is similar to that used for cloisonné enamels on copper, and it has a door opening outward.
When the charcoal fire has been lighted inside, the porcelain is placed upon an iron wheel, which is supported upon an iron fork, by which the porcelain is passed into the stove, and the fireman holds in his other hand an iron hook, so that he may be able to turn the wheel around in the fire to equalize the action of the heat. When the colors appear clear and bright the firing is reckoned to have been sufficient.
For large pieces the closed stove is employed. This stove is three feet high and nearly two feet and three-quarters in diameter. A double wall to hold the charcoal fire, the wall being perforated below for the entrance of air, surrounds it. The porcelain is introduced into the interior of the stove, while the man holds a circular shield to protect him from the heat of the fire. The top of the stove is then closed by a flat cover of yellow clay and closely luted. The firing takes a period of about twenty-four hours.
The process of firing the monochrome yellow, green, and purplish brown porcelains is the same as the above.”
19. Packing into container & cushioning with hay bundle 束草装桶
“After the porcelain has been taken out of the furnace it is arranged into four separate classes, which are known by the names of first-class color, second-class color, third-class color, and inferior ware, and the price is fixed accordingly at a high or low rate.
The porcelain of third-class color and the inferior ware are kept back for local sale.
The round ware of first-class color and the vases and sacrificial vessels of the first and second class are all wrapped up in paper and packed in round cases, there being packers whose duty it is to attend only to this work.
With regard to the round ware of second-class color, the dishes and bowls are tied together in bundles, each composed of ten pieces, which are wrapped round with straw and packed in round cases, for convenience of carriage to distant parts.
The coarser porcelain intended for ordinary use, which is distributed throughout the different provinces, is not packed in cases with straw, but only tied up in bundles with reeds and matting. From thirty or forty pieces up to sixty make a ‘load’ sufficient for a man to carry at each end of his yoke.
The ‘loads’ are packed inside with reeds and matting and bound round outside with strips of bamboo, ready to be conveyed either by water or by land as may be more convenient.
The workmen who do the packing are generally known by the name of mat-men. “
20. Thanksgiving Rituals 祀神酬原
“Jingdezhen, situated within the jurisdiction of Foliang Hsien, is only some ten or more li in circuit, surrounded by mountains and rivers, so as to form, as it were, an island, yet on account of its porcelain production merchants throng to it from all quarters.
The private kilns, between two and three hundred in number, exhibit a constant succession of flames and smoke the whole year round, and give employment to not less than several hundreds of thousands of workmen and assistants. The porcelain industry gives subsistence to an immense number of people whose life hangs on the success or failure of the furnace fires, and they are all devout in worship and sacrifice.
Their god, named T’ung, was once himself a potter, a native of the place. Formerly, during the Ming dynasty, when they were making the large dragon fish bowls, they failed in the firing year after year, although the eunuchs in charge inflicted the most severe punishments, and the potters were in bitter trouble.
Then it was that one of them, throwing away his life for the rest, leaped into the midst of the furnace, whereupon the dragon bowls came out perfect.
His fellow-workmen, pitying him and marveling, built a temple within the precincts of the imperial manufactory, and worshiped him there under the title of Genius of Fire and Blast.
Down to the present day the fame of the miracle is cherished, and the potters continue to worship him, not a day passing without reverential sacrificial offerings. Theatrical shows are also instituted in his honor, during which crowds of people fill the temple grounds. He is worshiped here as the tutelary gods of agriculture and land are in other parts of the empire.”
References
This compilation of Jingdezhen Porcelain information is based primarily on:
- The Pottery Workshop: Website, http://www.potteryworkshop.com.cn/Jingdezhen.asp
- Sten Sjostrand: Jingdezhen, The porcelain centre of the world, http://www.thewanlishipwreck.com/Jingdezhen.html
- Jingdezhen Municipal Government: Website, http://eng.jdz.gov.cn/Brief/introduction/201112/t20111201_122542.htm
- Tang Ying: Twenty Illustrations of the Manufacture of Porcelain, 1745